本革と合皮、見た目はよく似ていますが、それぞれの特徴は違います。
今回は本革と合皮の違いについてご紹介したいと思います。まずは、素材の違いからみていきましょう。
本革とは?
本革(天然皮革)とは、動物の皮をなめして革にしたものを指します。
牛や馬、豚、羊などの定番のものから、ヘビやトカゲといったエキゾチックレザーまで幅広い種類があります。
動物の皮はそのままの状態だと腐ってしまいますので、なめしを施して腐りにくくし、見た目や手触りを良くします。
もともとが生きた動物の皮ですので、キズやシワ、毛穴などが残っています。
合皮とは?
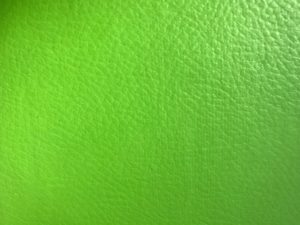
PUレザー
合皮とは、布地の上にポリウレタンやポリ塩化ビニル等の樹脂を塗布し、表面を本革に似せた素材のことです。
表示では、「合成皮革」と記されます。
ポリウレタンを使用したものはPUレザー、ポリ塩化ビニルはPVCレザーと呼ばれます。
プラスチックやビニールと同じようなものと考えると分かりやすいですね。
耐水性に優れ、汚れが付きにくいのが特徴です。
本革と合皮の違い
本革と合皮はそもそもの素材が違いますので、その特徴も違います。
一番の違いは、「本革は経年変化し、合皮は経年劣化する」ということです。
それぞれの特徴を詳しくみていきましょう。
本革の特徴
本革は、天然の表情や質感を楽しめる素材です。
動物の皮を加工しているため、始めからキズやシワがあることもあります。
特にこういった天然の表情を生かした革は、経年変化(エイジング)しやすく、使い込むほどに手になじみ、革独特の美しい風合いへと変化していきます。
本革製品は、メンテナンス次第で10年ほど持ちます。
本革の弱点は水分。
吸湿性があるため、長時間手で触れていても汗でべたつくということはありません。
ですが、その分汗や雨などに濡れるとしみになってしまうことがあります。
また、保管の仕方が良くないとカビが生えてしまうこともあります。
そうならないためにも、通気性の良い場所に保管し、定期的にオイルやクリームを塗るなどしてメンテナンスする必要があります。
合皮に比べると本革は価格が高く、重量は重めです。
合皮の特徴
一方で合皮は、安価で、同じ分量を使用していても本革より重量は軽めです。
見た目も本革と変わりませんが、質感などは違います。
プラスチックやビニールと同じ素材ですので、長時間手で触れていると汗でべたついてきます。
耐水性には優れていているため、雨でしみになるといったことはありません。
メンテナンスも本革に比べると簡単です。
汚れがついたら乾いた布や、薄めた洗剤に浸した布でふき取るだけです。
中には、ドライクリーニングできるものもあります。
合皮の寿命は約3年ほどです。
合皮によく使用されるポリウレタンは、合成された時点から劣化が始まっています。
空気中の水分と結合して加水分解されたり、紫外線や熱などの影響で徐々に分解され、劣化していきます。
表面がぬるぬるとした感じになったり、劣化が進むと表面がひび割れたり、ぼろぼろと剥がれて布地がむき出しの状態になったりします。
ここまでの内容を表にまとめてみましたので、こちらも参考にしてみてくださいね。
ここまで、本革と合皮、それぞれの特徴についてみてきました。
特に、本革は使ううちに色や風合いが深まっていくのに対して、合皮は徐々に劣化していく、というのが対照的です。
では最後に、本革と合皮の見分け方についてご紹介します。
本革と合皮の見分け方
最近の合皮はとても良く出来ていて、日々革に触れている私たちでも、一目見ただけでは本革と見分けがつかないものもあります。
本革と合皮を見分けるには、次の3点をチェックしてみることをおすすめします。
革の断面をみる
動物の皮は、太い繊維と細い繊維が複雑に絡まりあってできています。
そのため、断面を見ると、繊維質で毛羽立っています。
ベルトの穴やバッグの持ち手、内側などで断面をみてみましょう。
合皮の場合は、断面部分が厚い塗料でコーティングされていたり、布地が見えていることがあります。
革の表面をみる
本革は、もともと動物の皮膚。製革の工程で脱毛されますが、毛穴は残っています。
加工の仕方によっては毛穴が見えにくいものもあります。
一方、合皮は樹脂を加工したものですので、毛穴はありません。
革のすれた部分をみる
本革は染料や顔料で染めてあるため、すれた部分は色が落ちて、染色する前の色がでてきます。
合皮は、経年劣化してしまうため、すれるとひび割れたり剥がれたりして下の布地が見えます。
まとめ
今回は、本革と合皮の違いや見分け方についてご紹介しました。
使い始めは分からなくても、使い込むうちに徐々に違いがみえてきますね。
合皮は水分に強いため、雨の日や水場でも気にせず使うことが出来るというメリットがありますが、耐久性はあまりよくありません。
本革は値段も高く、メンテナンスや取り扱いに注意が必要ですが、長く使える分、愛着が湧く素材と言えるでしょう。
本革と合皮、それぞれにメリットデメリットがありますが、やはり私たちタンナーとしては、手間はかかっても長く使える本革製品をおすすめしたいところです。